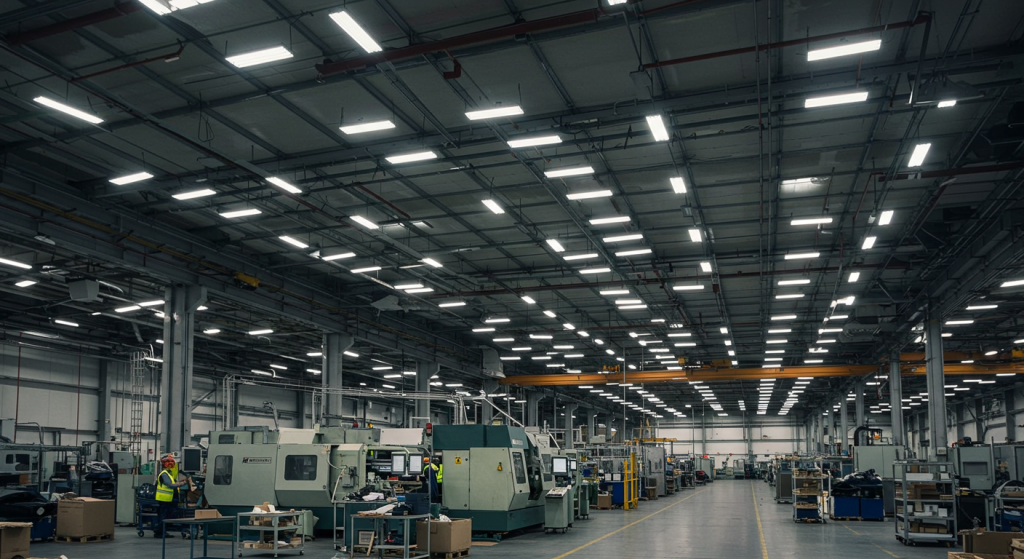
Step into a bustling factory—machinery humming, workers moving fast, and towering ceilings overhead. The bright, even light flooding the space comes from high bay lights, essential for keeping production safe and smooth. But not all high bay lights are created equal. LED high bay lights are transforming factories with their energy savings, durability, and superior performance. If you’re managing a factory and looking to cut costs while boosting safety and productivity, this post is for you. We’ll break down why LED high bay lights are a must, how they stack up against older options, and how to pick the right ones for your facility.
What Are LED High Bay Lights?
High bay lights are powerful fixtures designed for spaces with ceilings 15 to 40 feet high, such as factories, warehouses, or assembly plants. Their role is to deliver intense, uniform illumination to ensure workers can see clearly, operate machinery safely, and maintain quality control. Traditionally, factories relied on metal halide, high-pressure sodium, or fluorescent lights. Today, LED high bay lights are the top choice, offering lower energy use, longer lifespans, and better light quality.
Factories are tough environments. Lights may run 24/7, endure dust, vibrations, or extreme temperatures, and still need to perform flawlessly. LEDs are built to handle these challenges while keeping operational costs low. Unlike older technologies, they provide consistent light output without flickering or dimming, making them ideal for the high-stakes demands of industrial settings.
Why LEDs Are Essential for Factories
Factories consume massive amounts of energy, and lighting can account for 30-50% of the bill, especially with fixtures running long hours. LED high bay lights use 50-80% less power than traditional options, significantly reducing expenses. They also align with sustainability goals by cutting carbon emissions. Beyond savings, LEDs enhance safety by improving visibility and eliminating shadows, which reduces accidents and errors. Clear, high-quality light boosts worker focus, speeds up tasks, and improves output, keeping your production line on track. Let’s compare LEDs to traditional fixtures to see why they’re the best choice for factories.
LEDs vs. Traditional High Bay Lights: A Detailed Comparison
To understand why LEDs are dominating factory lighting, let’s compare them to metal halide, high-pressure sodium, and fluorescent lights. The differences in energy consumption, lifespan, and performance are striking.
Energy Consumption
LEDs excel at saving power. They produce the same—or brighter—light while using far less electricity. A 150-watt LED high bay can match a 400-watt metal halide, cutting energy use by over half. Studies show LEDs consume 50-80% less energy than traditional fixtures, translating to substantial savings on factory power bills.
Lifespan
Replacing bulbs in a factory is a logistical challenge, requiring lifts, downtime, and safety precautions. Metal halides last 10,000-20,000 hours, fluorescents around 30,000 hours. LEDs shine for 50,000-100,000 hours—10-20 years in a factory running 12 hours a day. This longevity slashes maintenance costs and keeps production uninterrupted. Research confirms LEDs are up to 10 times more durable than fluorescents.
Light Quality
Poor lighting can slow down factory work. Traditional fixtures, especially high-pressure sodium, have a low Color Rendering Index (CRI) of 60-70, making colors appear dull and details hard to discern. LEDs offer a CRI above 80, ensuring parts, labels, and hazards are clearly visible. This clarity is vital for quality control, precision assembly, and workplace safety.
Heat Output
Metal halides and high-pressure sodium lights generate significant heat, wasting energy and increasing cooling costs in warm environments. k-cob LED run cool, converting most of their energy into light. This reduces HVAC strain and keeps the factory comfortable, especially during hot shifts.
Upfront Costs vs. Long-Term Savings
LEDs carry a higher initial cost—$100-$200 per fixture compared to $50-$100 for metal halides. However, lower energy bills and minimal maintenance deliver a return on investment (ROI) in 1-2 years, particularly in high-usage factories. LEDs are the cost-effective choice over time due to reduced operating costs.
Here’s a comparison table for clarity:
Feature | LED High Bay | Metal Halide | Fluorescent |
---|---|---|---|
Energy Use | 50-80% less than traditional | High (400W typical) | Moderate (200-300W typical) |
Lifespan | 50,000-100,000 hours | 10,000-20,000 hours | 20,000-30,000 hours |
CRI | 80+ (excellent color rendering) | 60-70 (poor color rendering) | 70-80 (decent color rendering) |
Heat Output | Low (minimal waste heat) | High (significant waste heat) | Moderate |
Upfront Cost | Higher ($100-$200) | Lower ($50-$100) | Moderate ($75-$150) |
Maintenance | Minimal (long lifespan) | Frequent (bulb replacements) | Moderate (bulb replacements) |
Choosing the Right LED High Bay Lights for Your Factory
Not all LED high bay lights are the same. Selecting the right fixtures requires careful consideration of your factory’s needs. Here’s what to prioritize.
Lumens and Wattage
Lumens measure brightness, while wattage indicates power consumption. Aim for a high lumens-per-watt ratio—150-200 lm/W is excellent. For example, a 24,000-lumen LED high bay might use 150 watts, compared to 400 watts for a metal halide with similar output. Plan for 100-150 lumens per square foot for general factory areas, and 200+ for precision tasks like assembly or quality inspection.
Color Temperature
Color temperature, measured in Kelvin (K), affects the work environment. A 5000K-6000K light mimics daylight, keeping workers alert and making details sharp—ideal for most factory settings. A 4000K light is warmer, suitable for less intense areas like break rooms. Avoid temperatures below 4000K, as they can reduce focus and make spaces feel dim.
Beam Angle
Beam angle determines how light spreads. Narrow angles (60°) focus light downward, perfect for high ceilings or specific workstations like machining areas. Wider angles (90°-120°) cover open factory floors or assembly lines. Match the angle to your layout to eliminate shadows and ensure even coverage.
Durability
Factories are harsh environments, with dust, vibrations, and temperature extremes. Choose LEDs with an IP65 rating or higher for dust and moisture resistance. Robust heat sinks are essential for longevity, especially in high-heat areas near machinery or in unconditioned spaces. Fixtures should also withstand vibrations from heavy equipment.
Certifications
Opt for fixtures with ENERGY STAR or DesignLights Consortium (DLC) certifications, which ensure high quality and energy efficiency. These certifications often qualify for utility rebates, reducing upfront costs. UL (Underwriters Laboratories) listings confirm safety and compliance with industrial standards.
Smart Features
To stretch savings, consider LEDs with motion sensors, dimming, or daylight harvesting. Motion sensors cut power in idle areas, saving 50-75% in low-traffic zones like storage or maintenance areas. Daylight harvesting adjusts brightness based on natural light from windows or skylights, further reducing energy use. Smart controls can be programmed to match shift schedules, optimizing performance.
Real-World Impact of LED High Bay Lights
Switching to LED high bay lights transforms factory operations in measurable ways. Here’s how they deliver.
Cost Savings
Consider a factory with 50 high bay lights running 12 hours a day, five days a week. Switching from 400-watt metal halides to 150-watt LEDs could save $5,000-$7,000 annually on energy at $0.12 per kWh. Maintenance savings—fewer bulb replacements and no need for frequent lift rentals—add another $1,500, totaling $8,500 a year for a medium-sized facility. Many factories see ROI in 1-2 years, making LEDs a financially sound investment.
Safety and Productivity
High-CRI LEDs enhance visibility, making it easier to inspect parts, read gauges, or spot hazards. This reduces errors in assembly, machining, or quality control, saving time and materials. Clear lighting also prevents accidents, such as trips, falls, or equipment mishaps. Well-lit factories boost worker morale and focus, leading to faster production and fewer mistakes, which translates to better output and customer satisfaction.
Environmental Impact
LEDs reduce energy consumption, cutting greenhouse gas emissions. If every U.S. factory switched to LEDs, the environmental impact would be equivalent to removing thousands of cars from the road. Unlike fluorescents, LEDs contain no mercury, making disposal safer and more environmentally friendly. This supports corporate sustainability goals and compliance with green regulations.
Brand Reputation
Adopting eco-friendly practices appeals to customers, partners, and investors. Using LED high bay lights demonstrates a commitment to sustainability, which can attract environmentally conscious clients and enhance your brand’s standing in competitive markets. It’s a small change with a big impact on perception.
Challenges to Anticipate
LEDs aren’t without challenges. The upfront cost—$100-$200 per fixture—can be a hurdle, especially for large factories requiring dozens or hundreds of lights. Utility rebates and financing options can ease the burden, but budgeting is key. Low-quality LEDs may also disappoint, with issues like flickering, dimming, or early failure due to poor heat management. Stick with reputable brands like Philips, Cree, or Hykolity, and verify specs like lumens, CRI, and durability ratings.
Retrofitting older systems can be tricky. While many LEDs fit existing mounts, outdated wiring or incompatible fixtures may require upgrades. For complex installations, hiring a professional electrician ensures safety and compliance. Finally, integrating smart features like sensors or controls may involve a learning curve for staff, so plan for training to maximize benefits.
Steps to Transition to LED High Bay Lights
Ready to upgrade your factory’s lighting? Follow these steps for a smooth transition:
- Evaluate Your Needs: Calculate lumens based on your factory’s size, ceiling height, and tasks. Use 100-150 lumens per square foot for general areas, 200+ for precision work like assembly or inspection. A lighting professional can create a customized plan to ensure optimal coverage.
- Seek Rebates: Contact your utility provider for rebate programs, which can cover 20-50% of costs. Check industry resources for available incentives.
- Plan Installation: Many LEDs are plug-and-play, fitting existing mounts. For high ceilings, complex wiring, or large-scale projects, hire a licensed electrician to ensure safety and compliance.
- Test and Optimize: After installation, adjust dimmers, sensors, or smart controls to fine-tune performance. Monitor energy bills to confirm savings and make tweaks as needed.
- Engage Your Team: Explain how better lighting improves safety, comfort, and productivity to gain worker buy-in. Train staff on any smart features to ensure smooth operation.
Case Study: A Factory Lighting Overhaul
A 60,000-square-foot factory in Michigan replaced 70 metal halide fixtures with 150-watt LED high bay lights. Their annual energy costs dropped from $15,000 to $5,000, and maintenance expenses fell by $2,000 due to fewer bulb changes. A 25% utility rebate reduced their $12,000 upfront cost, delivering ROI in just 16 months. Workers reported fewer errors in assembly and felt safer under brighter, clearer light, boosting productivity by 6%. This real-world example highlights the transformative power of LEDs in industrial settings.
Additional Considerations for Factory Lighting
Beyond the basics, there are a few extra factors to keep in mind when choosing LED high bay lights for your factory.
Lighting Layout and Spacing
Proper spacing is critical to avoid dark spots or over-lit areas. High bay lights should be spaced based on ceiling height and beam angle. For example, at 20 feet, fixtures with a 90° beam angle might be spaced 15-20 feet apart for even coverage. A lighting plan from a professional can optimize placement, ensuring every workstation, aisle, and machine is well-lit without wasting energy.
Task-Specific Lighting
Factories often have varied tasks—assembly lines need bright, focused light, while storage areas can use less intense illumination. Consider using different fixtures or settings for different zones. For instance, high-lumen fixtures with narrow beams work well for precision tasks, while lower-lumen, wide-angle fixtures suit general areas. This zoning approach maximizes energy savings and performance.
Emergency and Backup Lighting
Factories must comply with safety codes, which often require emergency lighting for exits and critical areas. Some LED high bay lights come with built-in battery backups, ensuring illumination during power outages. Check local regulations to ensure your lighting plan meets OSHA or other standards.
Maintenance and Cleaning
Even with their long lifespan, LED fixtures need occasional cleaning to remove dust or debris, especially in factories with heavy machinery or particulate matter. Choose fixtures with smooth surfaces or protective covers for easy maintenance. Regular inspections can catch any issues, like loose mounts or wiring, before they become problems.
The Future of Factory Lighting
LED technology is advancing at a rapid pace. Newer models are achieving 200-250 lumens per watt, delivering more light with less power. Smart lighting systems are becoming more common, allowing factory managers to control fixtures via apps or integrate them with automation systems. For example, lights can dim during off-shifts or brighten when sensors detect activity, optimizing energy use. As energy regulations become stricter, LEDs will likely become the standard for industrial lighting. Factories that adopt them now will save significantly while staying ahead of compliance requirements.
Emerging trends also include tunable LEDs, which allow you to adjust color temperature throughout the day to mimic natural light cycles, potentially improving worker alertness and well-being. Additionally, advancements in optics are improving light distribution, reducing glare, and enhancing uniformity, which is particularly valuable in precision-driven factory environments.
Practical Tips for Maximizing LED Benefits
To get the most out of your LED high bay lights, consider these practical strategies:
- Conduct an Energy Audit: Before upgrading, assess your current lighting costs to establish a baseline. This helps quantify savings post-installation and justifies the investment to stakeholders.
- Phase the Transition: If budget constraints are an issue, replace fixtures in stages, starting with high-usage areas like production floors. This spreads costs while delivering immediate savings.
- Monitor Performance: Use energy management software to track consumption and identify opportunities for further savings, such as adjusting sensor settings or shift schedules.
- Partner with Suppliers: Work with reputable lighting suppliers who offer warranties, technical support, and guidance on rebates. This ensures you get high-quality fixtures and ongoing assistance.
- Document Savings: Keep records of energy and maintenance savings to share with leadership or investors, reinforcing the value of the upgrade and supporting future green initiatives.
Common Misconceptions About LED High Bay Lights
Despite their benefits, some misconceptions about LEDs persist. Let’s clear them up:
- “LEDs are too expensive”: While the upfront cost is higher, the long-term savings far outweigh the initial investment. Rebates and quick ROI make LEDs accessible for most factories.
- “LEDs don’t provide enough light”: Modern LEDs deliver high lumens, often outperforming traditional fixtures in brightness and uniformity. Proper selection ensures adequate illumination.
- “LEDs are complicated to install”: Many LEDs are designed for easy retrofitting, and professional installers can handle complex setups efficiently.
- “All LEDs are the same”: Quality varies widely. Choosing certified, reputable brands ensures durability and performance, avoiding issues with cheap alternatives.
Wrapping Up
LED high bay lights are a game-changer for factories, offering unmatched energy savings, durability, and light quality compared to traditional fixtures. They cut costs, enhance safety, and support sustainability, with savings that quickly offset the upfront investment. Whether you’re lighting a small workshop or a sprawling manufacturing plant, LEDs keep your factory bright, safe, and cost-effective. By choosing the right fixtures and planning a smooth transition, you can transform your facility’s performance and future-proof your operations.
FAQs
Q: How many LED high bay lights do I need for my factory?
A: It depends on size, ceiling height, and tasks. Aim for 100-150 lumens per square foot for general areas, 200+ for precision work. A lighting plan provides an exact count.
Q: Can I install LED high bay lights myself?
A: If they fit existing mounts and you’re comfortable with wiring, yes. For high ceilings or complex systems, hire an electrician for safety and compliance.
Q: Are LEDs worth the cost for factories?
A: Absolutely. Energy and maintenance savings deliver ROI in 1-2 years, and better lighting improves safety, productivity, and quality control.
Q: What’s the best color temperature for factory LEDs?
A: 5000K-6000K mimics daylight, ideal for focus and clarity in production areas. 4000K suits less intense spaces like break rooms.
Q: Do LEDs handle factory conditions like heat, dust, or vibrations?
A: Yes. Choose IP65-rated fixtures with robust heat sinks to withstand dust, vibrations, and temperatures from -22°F to 122°F.