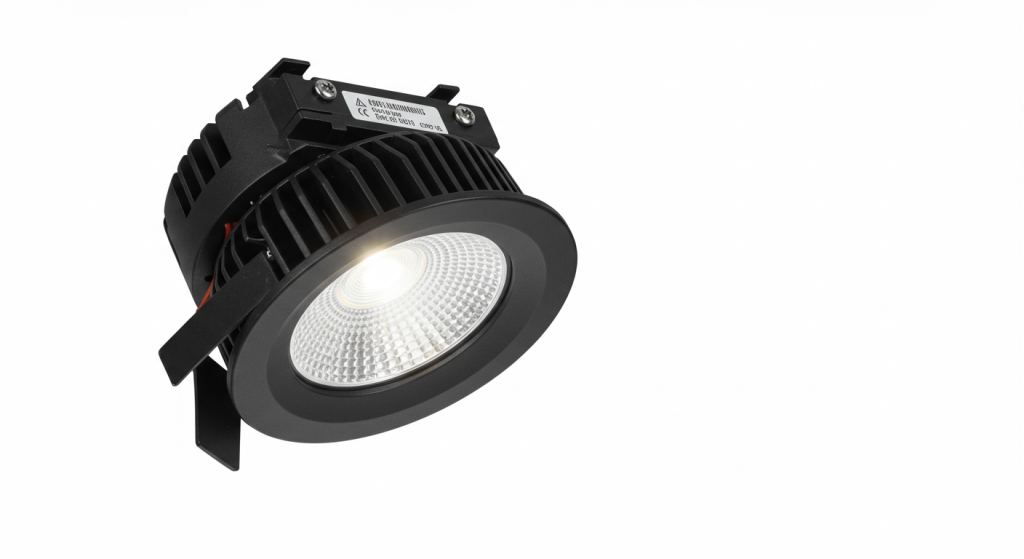
In a thriving factory or warehouse, where machines hum and workers move with precision, the recessed lights in the ceiling, delivering intense, focused illumination, are likely energy-efficient high power LED downlights. These fixtures are revolutionizing industrial spaces with their exceptional brightness, energy savings, and durability. If you’re managing an industrial facility and looking to cut costs while boosting safety and productivity, this post is your guide. We’ll explore why energy-efficient high power LED downlights are a game-changer, how they compare to traditional lighting, and how to select the right ones for your space, with practical insights to ensure a seamless transition.
What Are Energy-Efficient High Power LED Downlights?
Energy-efficient high power LED downlights are recessed fixtures installed flush into ceilings, designed to emit intense light output (typically 2,000 lumens or more per fixture) while consuming minimal energy. They’re ideal for high-ceiling industrial environments like factories, warehouses, distribution centers, or manufacturing plants, providing focused or broad illumination with a sleek, low-profile design. Unlike traditional high bay lights, these downlights excel in task-specific areas or spaces requiring both functionality and aesthetics. Previously, industrial spaces used incandescent, halogen, or compact fluorescent (CFL) downlights. Today, high power LED downlights lead the way, offering superior energy efficiency, longer lifespans, and exceptional light quality.
Industrial settings demand robust lighting—long operating hours, exposure to dust, vibrations, or extreme temperatures, and the need for precision and safety. Energy-efficient high power LED downlights are engineered to meet these challenges while drastically reducing energy costs, making them a perfect fit for demanding environments.
Why Energy-Efficient High Power LED Downlights Are Essential
Industrial facilities consume vast amounts of energy, with lighting often accounting for 30-50% of the electric bill, especially in spaces running 12-24 hours daily. At typical electricity rates of $0.12-$0.15 per kWh, costs can skyrocket. These LED downlights use 50-80% less power than traditional options, significantly cutting expenses. Many regions offer utility rebates covering 50-100% of upgrade costs, making the switch cost-effective. Beyond savings, their intense brightness enhances safety by improving visibility and reducing glare, minimizing accidents and errors. Focused, high-quality light boosts productivity in task-specific areas, and their durability ensures reliability in harsh conditions. Let’s compare these LEDs to traditional downlights to see why they’re the top choice for industrial spaces.
High Power LEDs vs. Traditional Downlights: A Head-to-Head Comparison
To understand why energy-efficient high power LED downlights are dominating industrial lighting, let’s compare them to incandescent, halogen, and CFL downlights. The differences in energy use, lifespan, and performance are substantial.
Energy Consumption
High power LED downlights are exceptionally efficient, converting most energy into light rather than heat. A 25-watt LED downlight delivering 2,500-3,500 lumens can match the brightness of a 100-watt incandescent or 42-watt CFL, cutting energy use by 50-75%. This efficiency translates to thousands in savings annually for large industrial facilities.
Lifespan
Replacing recessed bulbs in high-ceiling industrial spaces is a logistical challenge, often requiring lifts or scaffolding. Incandescents last 1,000-2,000 hours, halogens 2,000-4,000 hours, and CFLs 8,000-15,000 hours. High power LEDs shine for 25,000-50,000 hours—10-20 years in a facility with 12 hours of daily use—reducing maintenance costs and downtime.
Light Quality
Traditional downlights, especially CFLs, often have a Color Rendering Index (CRI) of 60-80, dulling colors and obscuring details. High power LED downlights offer a CRI of 90+, ensuring accurate color rendering, which is critical for tasks like quality control, equipment inspection, or reading labels. Selectable color temperatures (3500K-5000K) allow customization for different areas.
Heat Output
Incandescents and halogens generate significant heat, increasing cooling costs and discomfort in warm industrial environments. High power LEDs produce minimal heat, easing HVAC strain and maintaining comfortable conditions, especially in high-heat areas near machinery.
Upfront Costs vs. Long-Term Savings
High power LED downlights cost $50-$200 per fixture, compared to $10-$50 for CFLs or halogens. Utility rebates can cover 50-100% of costs, softening the initial investment. Energy and maintenance savings deliver a return on investment (ROI) in 1-2 years, making LEDs highly cost-effective long-term.
Here’s a comparison table:
Feature | High Power LED Downlight | Incandescent/Halogen | CFL |
---|---|---|---|
Energy Use | 50-75% less than traditional | High (100W typical) | Moderate (42W typical) |
Lifespan | 25,000-50,000 hours | 1,000-4,000 hours | 8,000-15,000 hours |
CRI | 90+ (excellent color rendering) | 90-100 (good rendering) | 60-80 (moderate rendering) |
Heat Output | Low (minimal waste heat) | High (significant waste heat) | Moderate |
Upfront Cost | Higher ($50-$200) | Lower ($10-$20) | Moderate ($20-$50) |
Maintenance | Minimal (long lifespan) | Frequent (bulb replacements) | Moderate (bulb replacements) |
Choosing the Right Energy-Efficient High Power LED Downlights
Selecting the best high power LED downlights requires tailoring to your facility’s needs and industrial conditions. Here’s what to prioritize.
Lumens and Wattage
Lumens measure brightness; wattage indicates power use. Aim for 80-100 lm/W for top efficiency. A 25-watt high power LED downlight delivering 2,500-3,500 lumens suits task areas like workstations, assembly lines, or inspection zones, while 4,000-5,000 lumens works for broader illumination in warehouses or production floors. Plan for 150-250 lumens per square foot for general areas, 400-600 for precision tasks like quality control or machining.
Color Temperature
Color temperature, measured in Kelvin (K), sets the workspace atmosphere. A 4000K-5000K light offers crisp, daylight-like clarity, ideal for factories, warehouses, or task-oriented areas where focus and detail are critical. A 3500K light provides a slightly warmer tone for mixed-use spaces like break rooms or administrative areas. Avoid temperatures below 3500K, as they can reduce alertness and clarity in high-intensity environments.
Beam Angle
Beam angle controls light spread. Narrow angles (30°-40°) focus light for specific tasks, such as illuminating machinery, workbenches, or quality control stations. Wider angles (60°-100°) provide broader coverage for open areas like storage zones or shipping docks. Choose based on your layout to minimize glare and ensure even illumination.
Durability
Industrial environments are harsh—dust, vibrations, moisture, and temperature extremes are common. Look for IP65 or higher ratings for dust and moisture resistance, essential for areas like loading docks or washdown zones. IC-rated downlights are safe for insulated ceilings, preventing heat buildup. Rugged, vibration-resistant housings ensure longevity near heavy machinery or in high-traffic areas.
Certifications
ENERGY STAR or DesignLights Consortium (DLC) certifications guarantee quality and efficiency, often qualifying for utility rebates. UL or ETL listings confirm safety, critical in industrial settings with strict codes. Fire-rated options meet building regulations, particularly in multi-level facilities or those with shared spaces.
Smart Features
Dimmable LEDs, 0-10V drivers, or smart controls (compatible with systems like Lutron or Zigbee) allow brightness adjustments and scheduling, saving energy during off-hours. Motion sensors or daylight harvesting adjust light based on occupancy or natural light, ideal for warehouses with variable activity. Emergency battery backups ensure compliance with safety codes, providing illumination during power outages.
Real-World Benefits for Industrial Spaces
Switching to energy-efficient high power LED downlights delivers transformative benefits. Here’s how.
Cost Savings
A facility with 50 high power downlights running 12 hours a day, five days a week, could save $3,000-$4,500 annually on energy by switching from 42-watt CFLs to 25-watt LEDs at $0.14 per kWh. Maintenance savings—fewer replacements and reduced labor—add $700, totaling $5,200 a year for a medium-sized facility. With rebates covering 50-100%, ROI often hits in under a year, especially in large factories or warehouses.
Safety and Productivity
High-CRI LEDs enhance visibility, making it easier to read labels, inspect components, or spot hazards like spills or equipment issues. This reduces errors in tasks like assembly, machining, or quality control and prevents accidents, such as trips or machinery mishaps. Intense, glare-free light boosts worker focus, speeding up production and improving accuracy, which enhances overall efficiency and output.
Environmental Impact
LEDs cut energy consumption, lowering greenhouse gas emissions. If industrial facilities widely adopted these downlights, the environmental impact would be substantial, supporting sustainability goals. Mercury-free LEDs simplify disposal compared to CFLs, reducing hazardous waste and aligning with eco-friendly practices.
Operational Reliability
Downtime is costly in industrial settings. LEDs’ long lifespan and durability minimize disruptions from bulb changes or failures, ensuring consistent lighting for critical operations. Their ability to perform in extreme conditions—cold storage, high-heat production areas, or dusty environments—makes them a reliable choice for demanding facilities.
Aesthetic and Functional Versatility
These downlights offer a sleek, modern look compared to bulky high bay lights, improving aesthetics in areas like showrooms, administrative offices, or mixed-use industrial spaces. Their intense illumination is ideal for task-specific zones, complementing broader lighting systems and enhancing overall functionality.
Challenges to Watch For
The upfront cost of high power LED downlights—$50-$200 per fixture—can be a barrier for large projects, though rebates significantly reduce this burden. Low-quality LEDs may flicker, dim prematurely, or have inconsistent color output, leading to poor performance or early replacement. Choose reputable brands like Philips, Cree, or Lithonia Lighting to avoid issues. Retrofitting older ceilings may require new cutouts, drivers, or junction boxes, and compatibility with existing dimming systems can be problematic. Industrial environments with strict safety codes may require additional certifications or fire-rated fixtures, adding complexity. Hiring a professional electrician ensures proper installation and compliance with local regulations.
How to Transition to Energy-Efficient High Power LED Downlights
Ready to upgrade your industrial lighting? Follow these steps for a smooth transition:
- Assess Your Space: Calculate lumens based on size and function. Aim for 150-250 lumens per square foot for general areas, 400-600 for task-specific zones like workbenches or inspection stations. A lighting professional can design a tailored plan to optimize coverage and performance.
- Check for Rebates: Contact your local utility provider for rebate programs, which can cover 50-100% of costs. Many utilities offer online tools or partner with contractors to simplify applications.
- Select Suppliers: Choose trusted suppliers with a range of industrial-grade high power LED downlights. Online platforms like 1000Bulbs or K-Cobled provide extensive options, while local distributors may offer on-site consultations.
- Plan Installation: Retrofit LEDs often fit existing cans, but new installations may require ceiling cutouts or wiring upgrades. For high-ceiling or complex projects, hire a licensed electrician to ensure safety and code compliance.
- Test and Optimize: After installation, adjust dimmers, sensors, or smart controls to fine-tune performance. Monitor energy bills to confirm savings and make adjustments as needed.
- Engage Staff: Highlight how brighter, clearer lighting improves safety, comfort, and productivity to gain worker buy-in, especially in task-heavy environments.
Case Study: A Manufacturing Plant Upgrade
A 30,000-square-foot manufacturing plant replaced 100 CFL downlights with 25-watt high power LED downlights in its assembly and quality control areas. Annual energy costs dropped from $9,000 to $2,500, and maintenance costs fell by $1,000 due to fewer replacements. A utility rebate covered 75% of the $15,000 upfront cost, yielding ROI in 14 months. Workers reported fewer errors in inspections and improved visibility, boosting productivity by 6%. The intense, focused lighting also enhanced safety, reducing minor accidents by 12%. This example highlights the impact of energy-efficient high power LED downlights in industrial settings.
Practical Considerations for Energy-Efficient High Power LED Downlights
Beyond the basics, consider these factors to maximize performance:
Task-Specific Lighting
Industrial facilities have diverse tasks—precision assembly demands intense, focused light, while storage areas need less. Use high-lumen, narrow-beam downlights for task zones and lower-lumen, wide-beam fixtures for general areas. This zoning approach optimizes energy use and performance.
Ceiling and Structural Constraints
Industrial ceilings may include insulation, ductwork, or beams, complicating installation. IC-rated downlights are essential for insulated ceilings to prevent heat buildup. Ensure fixtures are compatible with ceiling thickness and mounting systems, and verify load-bearing capacity for heavy-duty units.
Safety and Compliance
Industrial settings must meet strict safety codes, such as OSHA or IBC requirements. Fire-rated downlights are often required in multi-level facilities. Emergency battery backups or exit-sign-integrated downlights ensure compliance during power outages. Verify local regulations before installation.
Maintenance and Cleaning
Dust, grease, or debris can accumulate on fixtures in industrial environments, reducing light output. Choose downlights with smooth, sealed surfaces for easy cleaning. Schedule regular inspections to ensure lenses and housings remain clear and functional.
Integration with Existing Systems
High power downlights can complement existing high bay or overhead lighting systems. Coordinate beam angles and lumens to avoid over-lighting or dark spots. Smart controls can integrate downlights with broader lighting networks for unified operation.
The Future of Industrial Lighting
LED technology is advancing, with high power downlights achieving 100-150 lm/W, delivering more light with less power. Smart lighting systems are gaining traction, enabling integration with facility management systems or apps for remote control, scheduling, or occupancy-based adjustments. Tunable white LEDs, which shift color temperature to mimic natural light cycles, are emerging to enhance worker alertness and well-being. As energy regulations tighten and sustainability becomes critical, energy-efficient high power LEDs will become the standard for industrial lighting. Adopting them now ensures cost savings, compliance, and a competitive edge.
Common Misconceptions About Energy-Efficient High Power LED Downlights
Some misconceptions persist. Let’s address them:
- “High power LEDs are too expensive”: Upfront costs are higher, but rebates and long-term savings make them affordable, often paying for themselves in 1-2 years.
- “High power LEDs are overkill for industrial tasks”: Their intense brightness is ideal for precision work or large spaces, with adjustable options for versatility.
- “High power LEDs are hard to install in industrial settings”: Retrofit kits simplify upgrades, and professional installers handle complex ceiling or wiring challenges.
- “All high power LEDs are the same”: Quality varies widely. Certified brands ensure durability, consistent color, and performance in harsh environments.
Wrapping Up
Energy-efficient high power LED downlights are a smart choice for factories, warehouses, and manufacturing plants, offering unmatched brightness, energy savings, and durability. They cut costs, enhance safety, and boost productivity, with rebates making the transition affordable. Whether you’re lighting a small task area or a vast production floor, these fixtures deliver reliable, intense illumination in demanding conditions. By selecting the right downlights and planning a smooth installation, you can transform your facility’s performance and efficiency.
FAQs
Q: How many high power LED downlights do I need for my industrial space?
A: Depends on size and tasks. Aim for 150-250 lumens per square foot for general areas, 400-600 for task zones. A lighting pro can provide an exact count.
Q: Can I install high power LED downlights myself in an industrial setting?
A: If they fit existing cans and you’re comfortable with wiring, yes. For high ceilings or complex systems, hire a licensed electrician for safety.
Q: Are high power LED downlights worth the cost for industrial facilities?
A: Yes. Energy and maintenance savings, plus rebates covering 50-100%, deliver ROI in 1-2 years, with brighter lighting improving safety and productivity.
Q: What’s the best color temperature for high power LED downlights?
A: 4000K-5000K offers crisp clarity for factories and warehouses; 3500K suits mixed-use areas like break rooms.
Q: Do high power LED downlights handle industrial conditions like dust or vibrations?
A: Absolutely. Choose IP65-rated fixtures with rugged housings and heat sinks for dust, moisture, vibrations, and temperatures from -22°F to 122°F.